Agra is not just famous for its beautiful Mughal buildings, but also for its excellent leather shoes. The city represents a perfect blend of elegance and refinement, showcasing the Ganga-Jamuni culture. Recently, a team of DNN24 visited Agra’s largest shoe factory, Dawar shoes, to understand how leather shoes are made. This factory stands as an inspiration in the shoe industry. What makes Dawar Company special is not just its strong position in the leather business, but also its culture of treating everyone equally and spreading goodwill. The company works with many international shoe brands and makes high-quality shoes for them. In 2023, the Agra footwear industry received a special honor – the GI (Geographical Indication) tag, which proves how special and unique Agra’s leather shoes are.
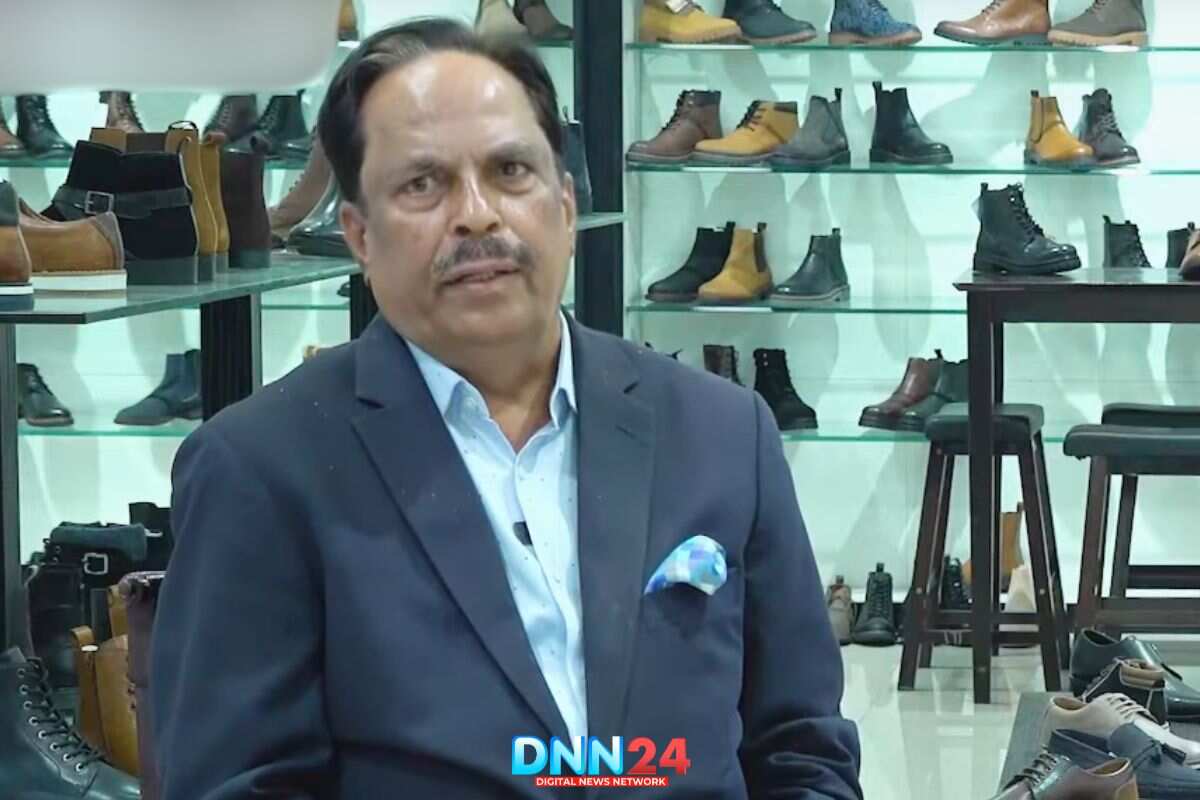
First Steps: Leather Selection and Quality Check
The journey of making a shoe starts with careful leather selection. Expert leather selectors come from outside to check the quality of leather. They look for any defects and make sure the leather matches the required style and specifications. Not all leather used in the factory comes from India – they source it from different places through their depot. The leather selectors have to be very careful about their work because the quality of leather decides how good the final shoe will be. They check things like leather texture, strength, and if it will work well for the specific shoe design they want to make. After selecting the right leather, it moves to the next stage of production.
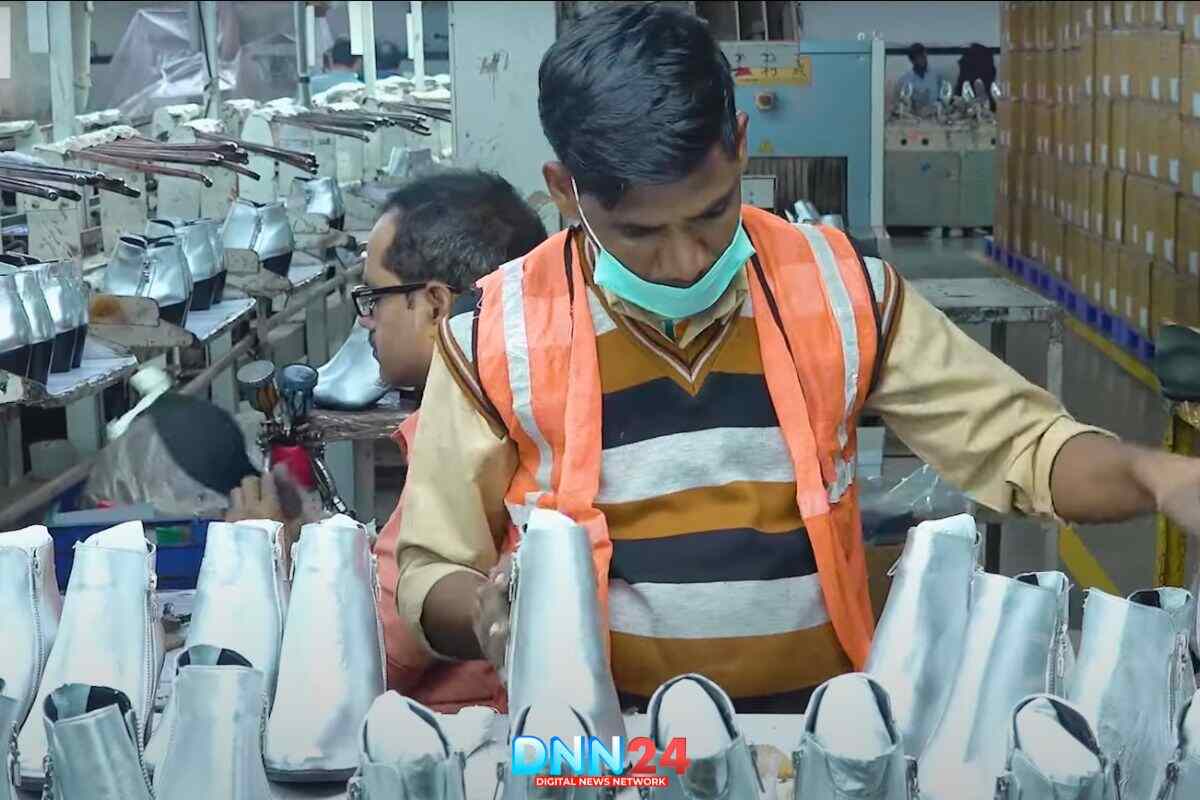
The Cutting Department: Where Shapes Come to Life
After leather selection, the material goes to the cutting department. Here, skilled workers cut the leather according to different shoe styles. This is a very important step because the way leather is cut affects how the final shoe will look and feel. The workers in this department are highly trained and use special tools to cut the leather perfectly. They follow specific patterns and measurements to make sure every piece matches exactly what the design needs. They must be careful not to waste leather and cut pieces that will fit together perfectly when the shoe is assembled. Each piece they cut will later become part of a shoe’s upper part or other components.
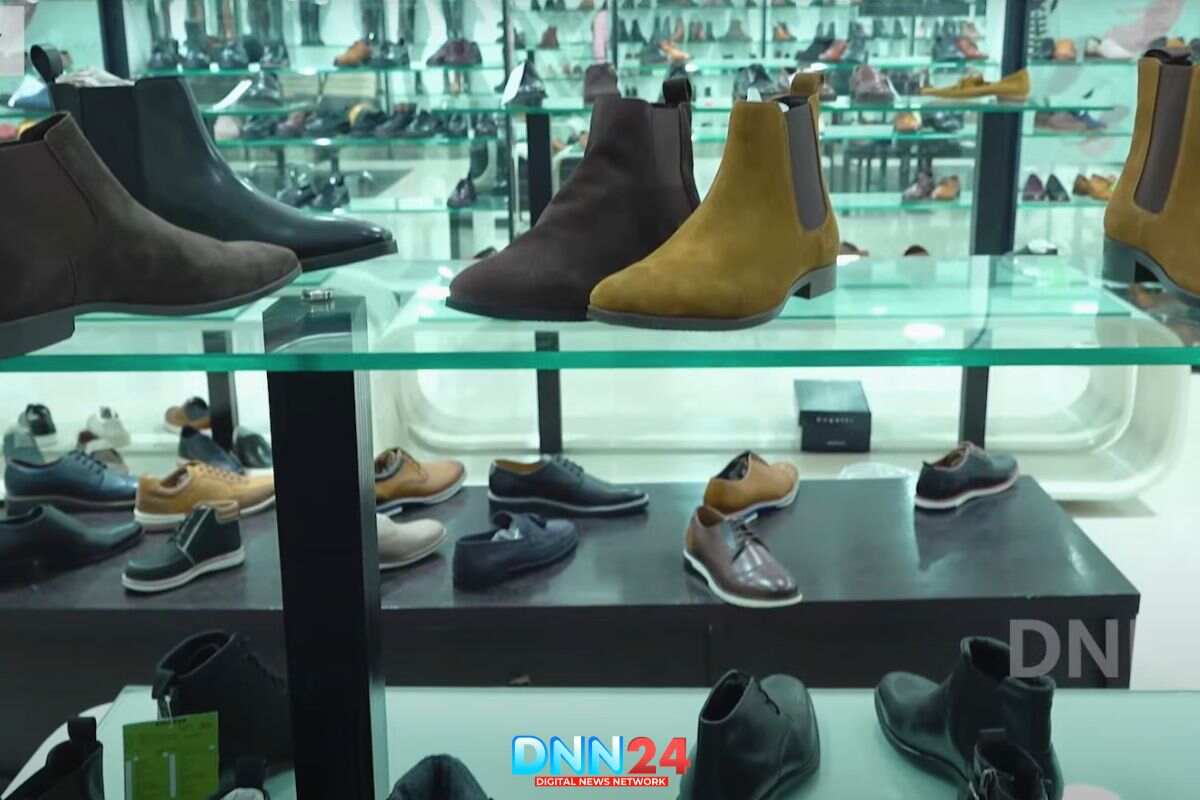
The Closing Department: Bringing Pieces Together
In the closing department, workers start putting the cut pieces of leather together. This is where the upper part of the shoe starts taking shape. The department handles tasks like stitching and preparing the leather components. Workers carefully join different parts using special machines and techniques. This stage requires a lot of skill because the pieces must be joined perfectly to make a comfortable and good-looking shoe. The work happens step by step, with each operation adding to the previous one. After the pieces are joined, they’re stored carefully before moving to the next stage.
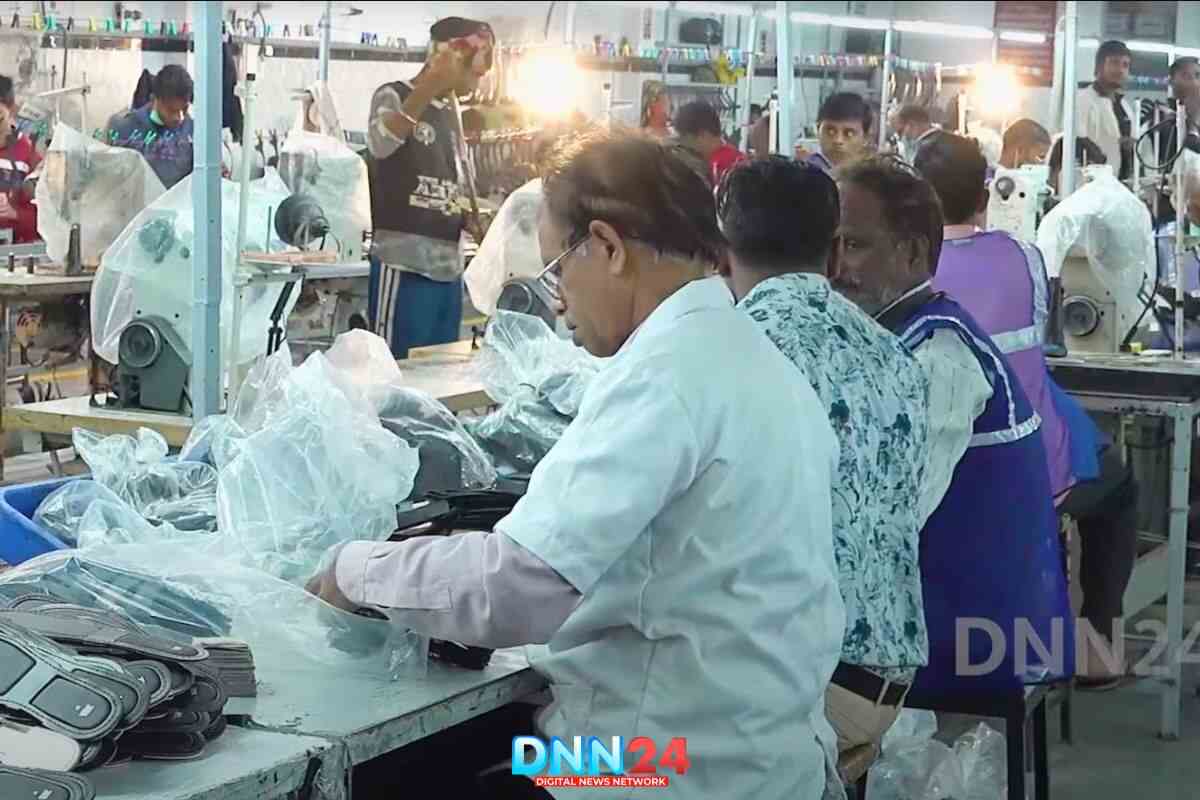
The Lasting Process: Shaping the Perfect Fit
Vishnu Sharma, who has worked at the factory for eight years, explains the lasting process. First, they bring out the shoe last (a foot-shaped mold). They apply paste to it and tie it with cord. Then comes the actual lasting process where the leather is shaped around the last. They do bonding work to give the shoe a good shape. Workers carefully remove any wrinkles to make sure the shoe looks perfect. They check each shoe thoroughly during this process. The next step involves making and attaching the sole. They use a sole press machine and wait for it to cool down before moving forward. This process is crucial for making comfortable shoes that fit well.
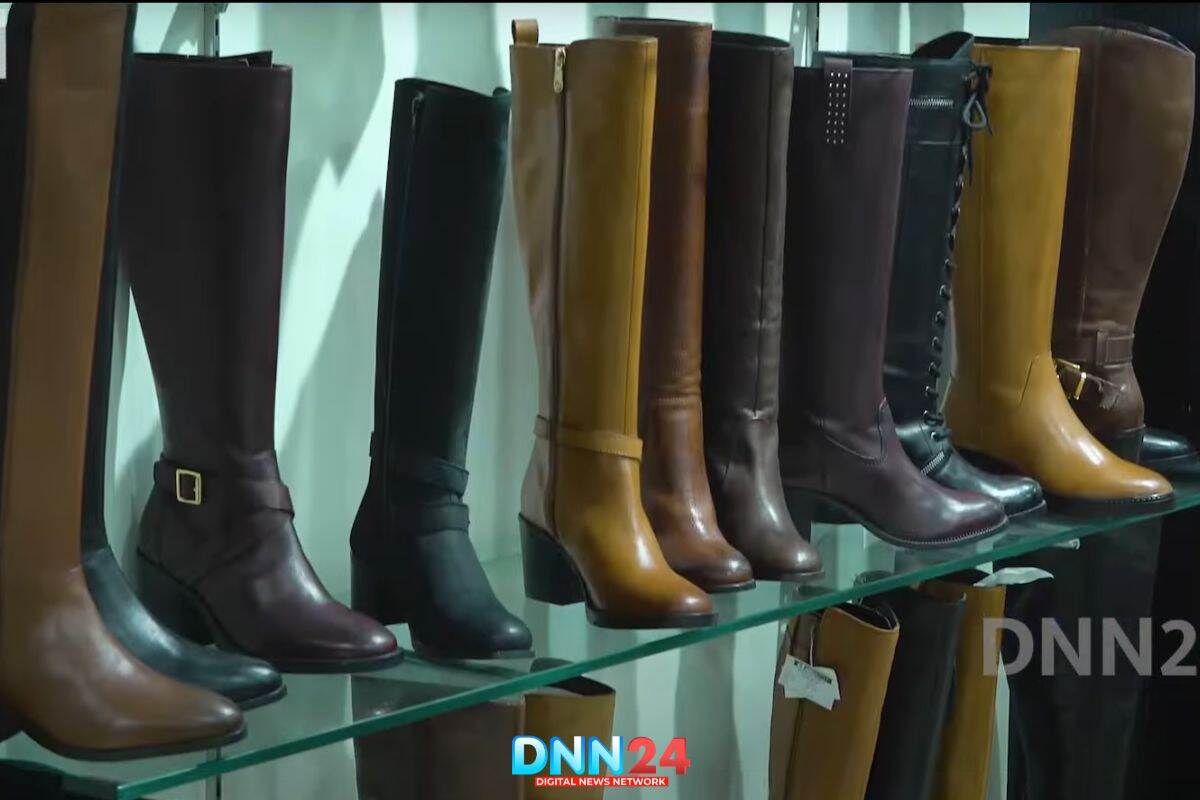
The International Connection
Dawar Company works with many European countries and makes shoes for their brands. The factory produces different types of shoes including jics, casual shoes, formal shoes, and special designs. They follow international quality standards and work closely with global shoe brands. Their ability to meet international standards while maintaining local craftsmanship makes them special. The company has built strong relationships with international partners over many years, which helps them stay updated with global shoe trends and technologies. This international exposure has helped them improve their shoe-making techniques while keeping their traditional strengths.
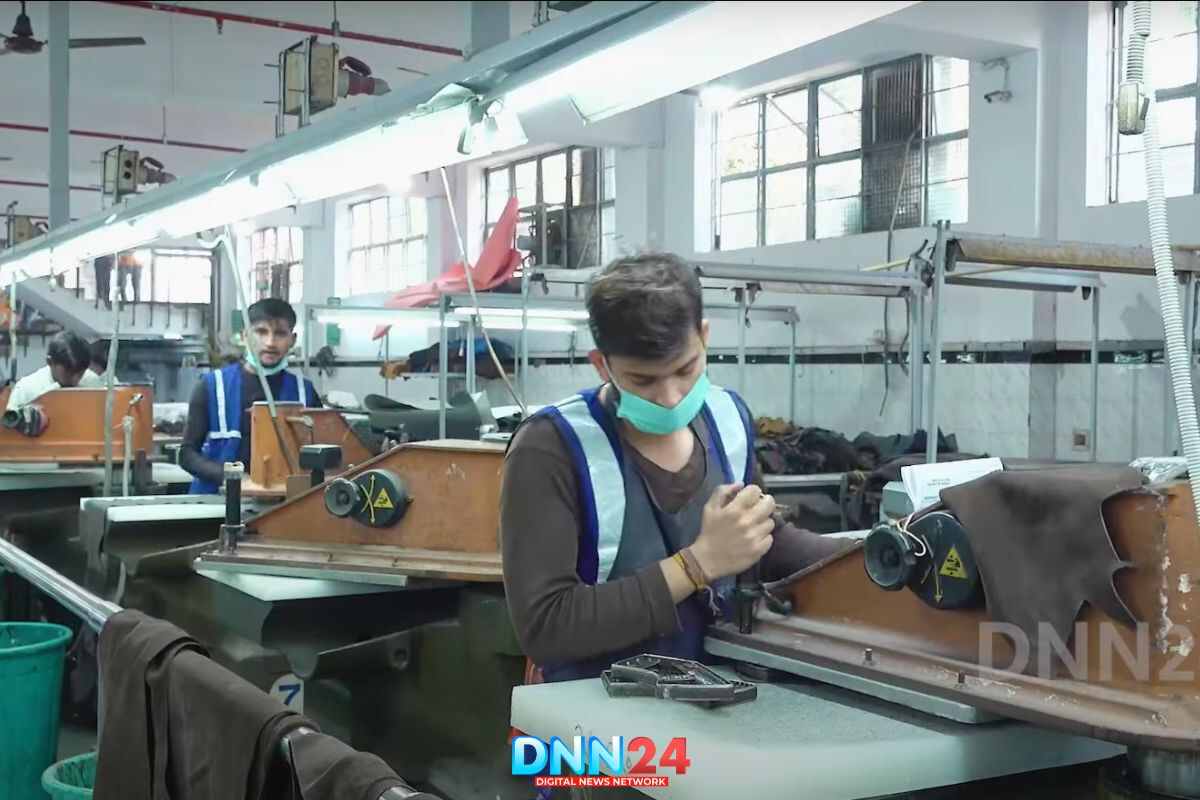
The People Behind the Shoes
The Dawar Group, started in 1977, now employs more than 2000 people in the factory. Many workers have been with the company for decades – like Saqil Khan (20 years), Pankaj (7 years), and Rizmani Usmani (12 years). The company values its workforce greatly and considers them their biggest strength. Many workers who started with small salaries of ₹1000-3000 now own cars and earn ₹10-25 lakhs per year after becoming graduates. The company has helped many people grow professionally and personally. They rarely need to recruit new people because workers stay with them for many years, showing how well the company treats its employees.
Also Read: Padma Shri Awardee Dr. Shyam Sundar Paliwal Transforming Rural India Through Piplantri Model
You can connect with DNN24 on Facebook, Twitter, and Instagram and subscribe to our YouTube channel.